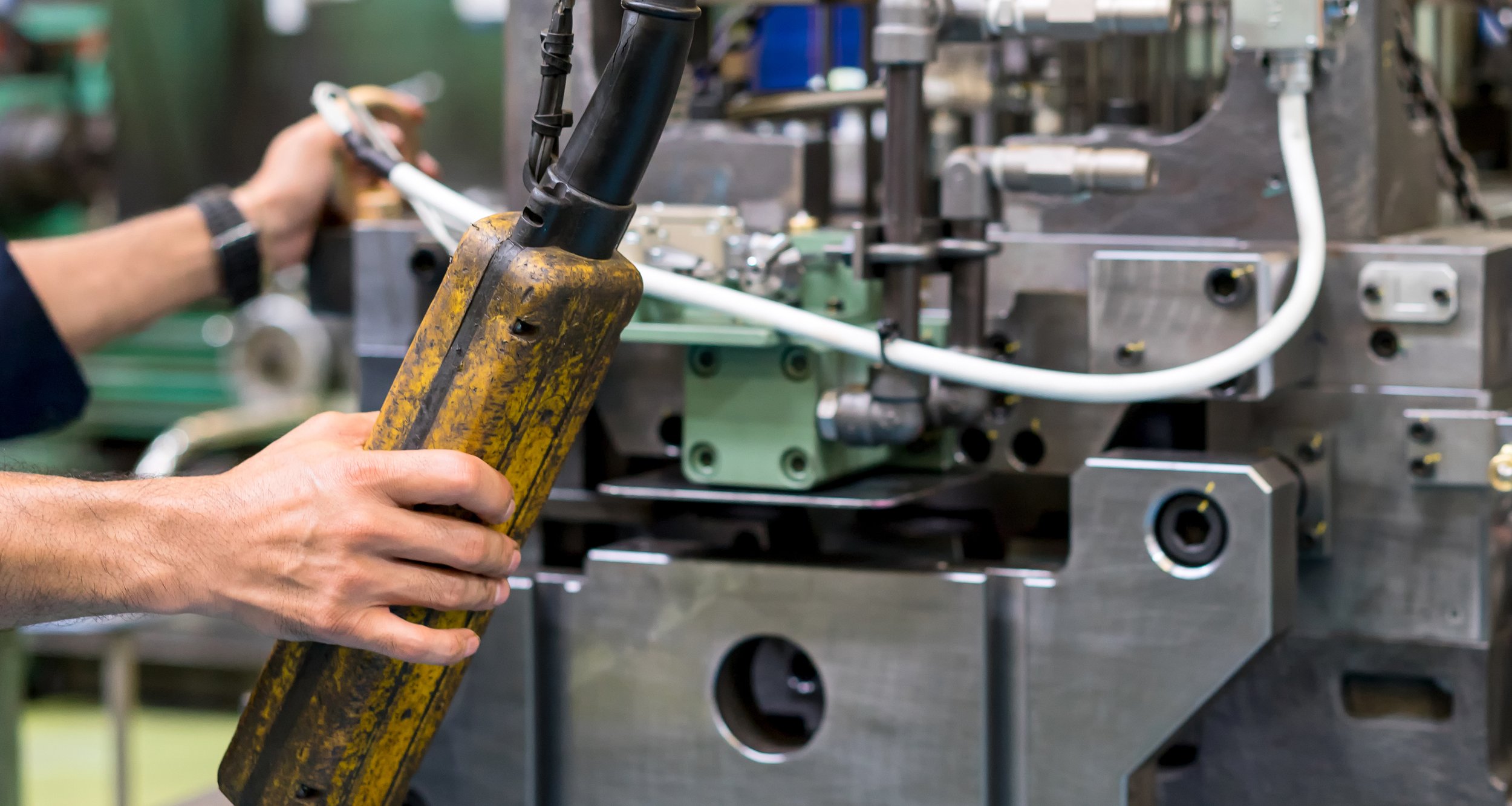
Product Design and Manufacturing
Manufacturing Support
Our toolbox of offerings extends to manufacturing processes and support. Whether we're collaborating with your resources or ours, we provide insight into potential risks due to interruptions in the supply chain, end-of-life (EOL) components, manufacturing delays due to scope creep, and schedule slips.
There are a variety of different tools and processes we use within the manufacturing support stage. Every project has its own goals and requirements – our product design and manufacturing teams help provide value by recommending which tools, processes, and manufacturing methods are an appropriate fit to meet the needs of your project.
VENDOR / TOOLING SUPPORT
Manufacturing is a significant investment, and the investment to start tooling is a big step for many clients. When the project is close to completion and ready for manufacturing handoff, we can help connect the right vendor for the client, aligning budgets and schedules. This includes CAD documentation and part inspection of first article inspection parts (FAI).
Identifying a tooling and manufacturing partner who has the experience and "fit" for the product is an important step. They must have the right experience and alignment with product requirements. There is also a wide range of production costs - so efficient manufacturing and assembly processes are key to identity. In product design and manufacturing, having effective communication between teams is an important factor for success in the design process. We bridge manufacturing with our clients, collaborating with vendors to make any necessary changes with manufacturers to reduce manufacturing costs and improve both the assembly process and production processes.
PART INSPECTION
Inspecting finished parts and assemblies is a crucial part of the development process. Checking parts against drawings, reviewing fitments, and verifying CFMs is a process that can't be overlooked. Specified requirements, product quality standards, and design specifications need to be met in order to ensure overall reliability and successful design execution. If tolerances and specifications do not meet the drawings or required standards, updates will be needed for successful integration into the final product.
Building a quality product involves executing the production process and confirming the correct materials, tight tolerances, and overall functionality are achieved. Successful product performance will depend on the care and evaluation given during this part inspection phase to provide quality control on all produced product components.
FAQ’s
-
This question is asked often, and it is really difficult to pinpoint an answer because there are so many variables in delivering product engineering services, from product complexity, testing, user/focus group feedback, certifications, etc. In a perfect world, we recommend our clients allocate up to 8-15 weeks, depending on the complexity and the speed at which client feedback.
2-3 weeks for research/strategy,
3-4 weeks for concept development,
3-5 weeks for mechanical development/implementation,
3-4 weeks for prototyping.
In most cases, this doesn’t mean you are ready for tooling!
We'd be happy to share a case study of our process and work - walk through a timeline from start to finish to give you a more realistic timeline for your project.
-
In many cases, especially larger corporations producing products an in-house creative team exists. One of our strengths is the ability to adapt and challenge the status quo without compromising the creative value you need. A collaborative work process helps with designing products as it involves creating an environment to share and build on each other's ideas. Our product designers and engineering teams thrive when more resources are available to work with - we look forward to seeing how we can work together to help build innovative solutions. Whether it's a marketing point person directing brand development, a CFM specialist, or a manufacturing engineer - we believe our adaptive design process is structured well for the collaborative effort with your teams.
-
This question comes up frequently, and giving an exact estimate can be challenging due to the presence of several variables. Nevertheless, in many cases, we segment project estimates into distinct phases to ensure transparency and clarity in assessing the required effort. The design process and product development cycle can look vastly different depending on the complexity of a project and if there are multiple products to design.
-
One of the big goals for any project is to stay on budget. Manufacturing costs and the production process take up a large part of a project's budget, and our design team looks at efficiencies throughout the entire product development process. On the front end of development, design decisions early on in the concept phase play a critical role in achieving a solution that will translate well to efficient manufacturing operations. Implementing Design for Manufacturing (DFM) practices as early as possible will help save costs later on in the manufacturing process. We often work closely with a production engineer and manufacturing engineers to make sure we are designing components with proper manufacturing principles as early as possible. This ultimately will provide cost-effective design solutions that can be executed by manufacturing processes with cost-reduction techniques.
-
Yes. We understand the hurdles and complexities that come with launching a new startup or building a brand — it's no small feat. Recognizing the various challenges, we, as partners, are prepared to contribute our design services as a form of capital tailored to the specific needs of the venture.
-
This varies. Our standard payment terms are net 15 days. We offer flexibility to our long-standing clients and established relationships, allowing for a net payment period of 30 days or more.
-
At the beginning of any project, many preconceived ideas won't materialize or reach fruition. And the problem-solving process in new product development is rarely linear. Our objective with any client project is to offer transparency throughout the process, including risks and opportunities. With a clear goal of providing you with a solution that meets the business objectives and products your customers will love. Our product designers and design teams quickly iterate ideas and craft solutions to incorporate successful DFM processes.